Discovering Cutting-Edge Foam Control Technologies for Lasting Practices
Discovering Cutting-Edge Foam Control Technologies for Lasting Practices
Blog Article
The Role of Foam Control in Enhancing Item Top Quality and Performance
Foam control is an often-overlooked yet important part in the quest of product high quality and functional efficiency throughout diverse industries. By successfully handling foam development, firms can not just improve the consistency of their formulas yet also tackle functional obstacles that can restrain performance. This discussion will certainly discover the multifaceted impact of foam on both product stability and production procedures, elevating crucial concerns regarding the strategies that can be used to optimize foam control. As we think about these effects, it comes to be clear that the risks are greater than they could originally appear.

Recognizing Foam Development
Foam development is a complicated phenomenon that can considerably affect product quality and operational efficiency across numerous industries. Recognizing these variables is essential for taking care of foam properly.
The liquid's viscosity and surface area stress play pivotal duties in foam stability. Surfactants, as an example, can minimize surface area tension, advertising bubble formation however additionally improving foam security, which can be problematic in certain applications. Furthermore, mechanical frustration, temperature variations, and the existence of impurities can aggravate foam generation, making it important to check these aspects during production procedures.
Industries such as food and beverage, drugs, and chemical production should be particularly cautious relating to foam control. By realizing the underlying systems of foam formation, organizations can execute targeted approaches to mitigate its results, thus preserving functional effectiveness and making certain consistent product performance.
Influence on Product Quality
The existence of foam can dramatically jeopardize item quality throughout different industries. In manufacturing processes such as food and beverage, pharmaceuticals, and cosmetics, excessive foam can cause irregular product formulations. As an example, in food production, foam might catch air, influencing texture and taste, which can inevitably modify customer assumption and contentment.
In addition, foam can impede the uniformity of coatings and paints, causing problems like bubbles and uneven coatings. In pharmaceutical applications, foam can hinder the accurate application of fluid medicines, possibly influencing therapeutic efficiency and client security. These high quality problems not only diminish completion item's appeal however can also result in costly recalls and damage to brand reputation.
In addition, the presence of foam can complicate quality control procedures, making it challenging to attain regular results and exact measurements. Reliable foam control not just reduces these risks but additionally improves total item top quality by making certain that formulas meet stringent sector criteria. By buying foam control approaches, business can protect their items, improve client satisfaction, and preserve an affordable side in the market.
Functional Difficulties From Foam
Effective procedures in various sectors can be significantly interrupted by the existence of foam, which positions numerous difficulties throughout production processes. Foam can hinder blending and response times, hampering the effectiveness of chemical procedures. In industries such as food and beverage, foam formation can lead to unreliable fill degrees, causing product waste and incongruities in packaging.
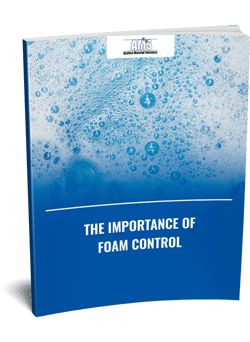
In environments where health is extremely important, such as pharmaceuticals and food handling, foam can make complex cleansing procedures, creating surprise storage tanks for pollutants. This not only elevates high quality concerns but likewise can result in compliance concerns with regulatory standards.
Furthermore, the psychological influence on operators can not be forgotten; excessive foam can create a chaotic workplace, bring about decreased spirits and productivity. In recap, dealing with the operational difficulties positioned by foam is crucial to maintaining effectiveness and product top quality in numerous industries.
Approaches for Effective Foam Control
Exactly how can industries efficiently mitigate the challenges positioned by foam? Effective foam control techniques are vital for improving product quality and operational performance. One key method is using defoamers, which are chemical representatives designed to get rid of or minimize foam formation. Picking the appropriate defoamer needs a detailed understanding of the particular process problems and the materials involved.
Along with chemical options, process optimization plays a critical role in foam monitoring. Industries can examine and adjust parameters such as blending stress, temperature, and speed to reduce foam generation. Carrying out equipment modifications, like setting up foam-breaking tools or adjusting storage tank style, can further help in reducing foam degrees.
Regular tracking and analysis of foam habits within production procedures are also vital. Making use of sophisticated sensors and analytics can offer real-time data, enabling prompt interventions and adjustments. Staff training is similarly crucial; guaranteeing that employees are knowledgeable regarding foam dynamics and control methods can bring about proactive foam monitoring.
Study and Market Applications
While lots of markets deal with unique difficulties associated with foam control, study reveal that Look At This tailored methods can dramatically enhance both item quality and operational effectiveness. In the pharmaceutical sector, for example, a leading producer executed a custom-made foam control strategy that lowered foam formation during fermentation procedures. This development not only enhanced yield by 15% however likewise minimized contamination dangers, making sure higher product integrity.
Likewise, in the food and beverage sector, a significant dairy manufacturer challenged excessive foam throughout pasteurization - Foam Control. By introducing a specialized antifoam agent, they lowered processing time by 20%, which directly equated to boosted throughput and minimized power intake. The application of foam control gauges ensured constant product texture and taste, strengthening brand name loyalty
In the chemical production industry, a case study highlighted the successful application of foam control in wastewater treatment procedures. The implementation of a real-time monitoring system permitted drivers to adjust antifoam dose dynamically, resulting in a 30% reduction in chemical use and improved effluent quality.
These study illustrate the varied applications of foam control across markets, highlighting its essential function in improving product quality and operational performance.
Conclusion
Finally, efficient foam control is integral to boosting item quality and functional effectiveness across different sectors. By addressing foam formation, organizations can reduce the unfavorable impacts on formulations, appearance, and application accuracy. Carrying out targeted foam monitoring strategies not just lowers handling delays and waste yet additionally strengthens devices integrity. Ultimately, prioritizing foam control adds to boosted efficiency, protecting brand name reputation, and raising consumer contentment, highlighting its importance in quality control within producing procedures.
Foam control is an often-overlooked yet essential element in the quest of item top quality and operational efficiency throughout diverse sectors. Team training is equally essential; ensuring that personnel are experienced regarding foam characteristics and control methods can lead to aggressive foam administration.
While several markets encounter one-of-a-kind difficulties associated to foam control, instance article researches expose that tailored strategies can significantly improve both product top quality and functional efficiency (Foam Control). In click reference the pharmaceutical sector, for instance, a leading supplier carried out a custom-made foam control method that minimized foam development throughout fermentation procedures.In verdict, effective foam control is indispensable to boosting product high quality and functional performance across various industries
Report this page